Exactly how to Identify What is Porosity in Welding and Improve Your Strategy
Exactly how to Identify What is Porosity in Welding and Improve Your Strategy
Blog Article
Porosity in Welding: Identifying Common Issues and Implementing Ideal Practices for Prevention
Porosity in welding is a pervasive concern that often goes undetected until it causes considerable problems with the honesty of welds. In this discussion, we will explore the key elements contributing to porosity development, examine its destructive effects on weld performance, and review the finest techniques that can be adopted to reduce porosity incident in welding procedures.
Common Sources Of Porosity

Another frequent culprit behind porosity is the existence of contaminants externally of the base metal, such as oil, grease, or corrosion. When these pollutants are not effectively removed prior to welding, they can evaporate and end up being caught in the weld, creating flaws. Additionally, using filthy or wet filler products can introduce contaminations into the weld, adding to porosity issues. To alleviate these usual root causes of porosity, comprehensive cleansing of base steels, correct protecting gas selection, and adherence to optimum welding parameters are necessary methods in accomplishing high-grade, porosity-free welds.
Effect of Porosity on Weld High Quality

The visibility of porosity in welding can dramatically endanger the architectural stability and mechanical buildings of bonded joints. Porosity creates spaces within the weld steel, deteriorating its total toughness and load-bearing capacity. These gaps act as anxiety concentration points, making the weld a lot more prone to cracking and failure under applied lots. In addition, porosity can reduce the weld's resistance to deterioration and other environmental elements, even more decreasing its durability and efficiency.
Welds with high porosity degrees often tend to display reduced effect toughness and reduced ability to warp plastically before fracturing. Porosity can hinder the weld's capacity to effectively transmit pressures, leading to early weld failing and possible safety and security threats in critical structures.
Best Practices for Porosity Prevention
To boost the structural stability and quality of bonded joints, what specific procedures can be applied to decrease the event of porosity check these guys out throughout the welding procedure? Using the appropriate welding technique for the certain product being welded, such as changing the welding angle and gun position, can further avoid porosity. Regular assessment of welds and instant removal of any concerns recognized throughout the welding process are vital techniques to prevent porosity and generate high-grade welds.
Importance of Proper Welding Techniques
Executing correct welding methods is paramount in guaranteeing the structural honesty and quality of welded joints, building on the structure of efficient porosity avoidance actions. Welding methods directly affect the total toughness and durability of the welded structure. One vital element of proper welding techniques is preserving the proper warm input. Extreme warm can lead to enhanced porosity due to the entrapment of gases in the weld pool. On the other hand, not enough warm may lead to insufficient blend, producing possible powerlessness in the joint. Furthermore, using the suitable welding specifications, such as voltage, existing, and travel speed, is essential for accomplishing sound welds with very little porosity.
Furthermore, the choice of welding process, whether it be MIG, TIG, or stick welding, should straighten with the specific requirements of the task to make certain ideal results. Correct cleansing and preparation of the base steel, along with choosing the right filler product, are likewise vital components of proficient welding strategies. By sticking to these finest practices, welders can decrease the danger of porosity formation check out here and produce top quality, structurally audio welds.
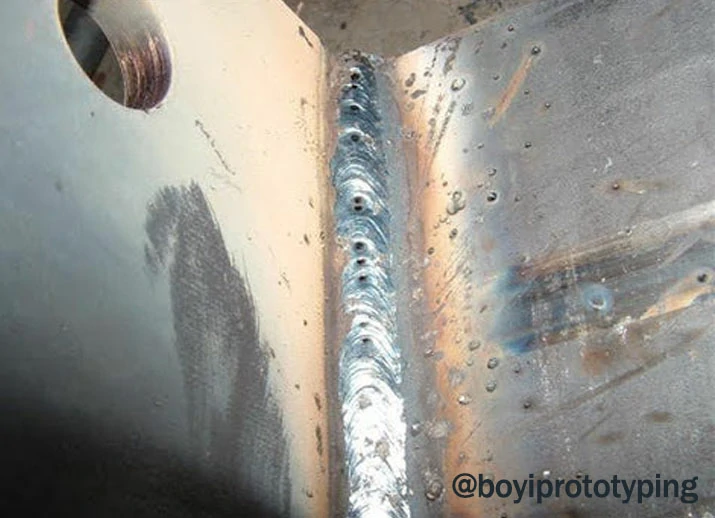
Examining and High Quality Control Steps
Examining treatments are essential to identify and prevent porosity in welding, ensuring the stamina and toughness of the last item. Non-destructive testing approaches such as ultrasonic screening, radiographic screening, and aesthetic evaluation are typically employed to identify possible flaws like porosity.
Carrying out pre-weld and post-weld evaluations is also essential in preserving quality assurance criteria. Pre-weld evaluations entail confirming the materials, equipment setups, and cleanliness of the workplace to avoid contamination. Post-weld assessments, on the other hand, examine the final weld for any type of defects, consisting of porosity, and confirm that it fulfills specified requirements. Implementing a thorough high his comment is here quality control strategy that includes detailed testing treatments and inspections is vital to reducing porosity problems and ensuring the general top quality of bonded joints.
Final Thought
In verdict, porosity in welding can be an usual issue that impacts the high quality of welds. By determining the usual sources of porosity and implementing best practices for prevention, such as appropriate welding methods and testing steps, welders can ensure excellent quality and reputable welds. It is important to focus on avoidance techniques to decrease the incident of porosity and maintain the stability of bonded structures.
Report this page